FPC的PCBA组装焊接流程,不同于硬性电路板
FPC又称柔性电路板,FPC的PCBA组装焊接流程与硬性电路板的组装有很大的不同,因为FPC板子的硬度不够,较柔软,如果不使用专用载板,就无法完成固定和传输,也就无法完成印刷、贴片、过炉等基本SMT工序。
本文引用地址:http://www.amcfsurvey.com/article/201804/377988.htm一.FPC的预处理
FPC板子较柔软,出厂时一般不是真空包装,在运输和存储过程中易吸收空气中的水分,需在SMT投线前作预烘烤处理,将水分缓慢强行排出。否则,在回流焊接的高温冲击下,FPC吸收的水分快速气化变成水蒸气突出FPC,易造成FPC分层、起泡等不良。
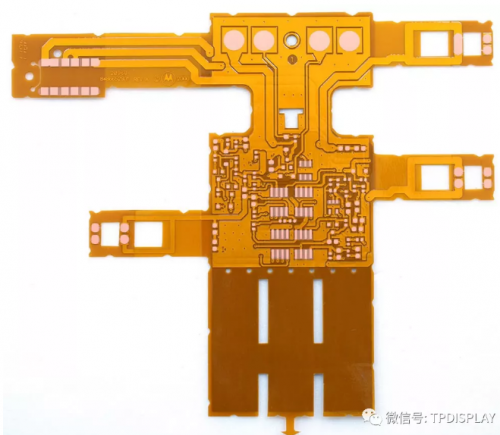
预烘烤条件一般为温度80-100℃时间4-8小时,特殊情况下,可以将温度调高至125℃以上,但需相应缩短烘烤时间。烘烤前,一定要先作小样试验,以确定FPC是否可以承受设定的烘烤温度,也可以向FPC制造商咨询合适的烘烤条件。烘烤时,FPC堆叠不能太多,10-20PNL比较合适,有些FPC制造商会在每PNL之间放一张纸片进行隔离,需确认这张隔离用的纸片是否能承受设定的烘烤温度,如果不能需将隔离纸片抽掉以后,再进行烘烤。烘烤后的FPC应该没有明显的变色、变形、起翘等不良,需由IPQC抽检合格后才能投线。
二.专用载板的制作
根据电路板的CAD文件,读取FPC的孔定位数据,来制造高精度FPC定位模板和专用载板,使定位模板上定位销的直径和载板上的定位孔、FPC上定位孔的孔径相匹配。很多FPC因为要保护部分线路或是设计上的原因并不是同一个厚度的,有的地方厚而有的地方要薄点,有的还有加强金属板,所以载板和FPC的结合处需要按实际情况进行加工打磨挖槽的,作用是在印刷和贴装时保证FPC是平整的。载板的材质要求轻薄、高强度、吸热少、散热快,且经过多次热冲击后翘曲变形小。常用的载板材料有合成石、铝板、硅胶板、特种耐高温磁化钢板等。
三.生产过程.
我们在这里以普通载板为例详述FPC的SMT要点,使用硅胶板或磁性治具时,FPC的固定要方便很多,不需要使用胶带,而印刷、贴片、焊接等工序的工艺要点是一样的。
1. FPC的固定:
在进行SMT之前,首先需要将FPC精确固定在载板上。特别需要注意的是,从FPC固定在载板上以后,到进行印刷、贴装和焊接之间的存放时间越短越好。载板有带定位销和不带定位销两种。不带定位销的载板,需与带定位销的定位模板配套使用,先将载板套在模板的定位销上,使定位销通过载板上的定位孔露出来,将FPC一片一片套在露出的定位销上,再用胶带固定,然后让载板与FPC定位模板分离,进行印刷、贴片和焊接。带定位销的载板上已经固定有长约1.5mm的弹簧定位销若干个,可以将FPC一片一片直接套在载板的弹簧定位销上,再用胶带固定。在印刷工序,弹簧定位销可以完全被钢网压入载板内,不会影响印刷效果。
方法一(单面胶带固定):用薄型耐高温单面胶带将 FPC 四边固定在载板上,不让 FPC 有偏移和起翘,胶带粘度应适中,回流焊后必须易剥离,且在FPC上无残留胶剂。如果使用自动胶带机,能快速切好长短一致的胶带,可以显著提高效率,节约成本,避免浪费。
方法二(双面胶带固定):先用耐高温双面胶带贴在载板上,效果与硅胶板一样,再将 FPC 粘贴到载板,要特别注意胶带粘度不能太高,否则回流焊后剥离时,很容易造成FPC撕裂。在反复多次过炉以后,双面胶带的粘度会逐步变低,粘度低到无法可靠固定FPC时必须立即更换。此工位是防止FPC脏污的重点工位,需要戴手指套作业。载板重复使用前,需作适当清理,可以用无纺布蘸清洗剂擦洗,也可以使用防静电粘尘滚筒,以除去表面灰尘、锡珠等异物。取放FPC时切忌太用力,FPC较脆弱,容易产生折痕和断裂。
2. FPC的锡膏印刷:
FPC对焊锡膏的成分没有很特别的要求,锡球颗粒的大小和金属含量等以FPC上有没有细间距IC为准,但 FPC对焊锡膏的印刷性能要求较高,焊锡膏应具有优良的触变性,焊锡膏应该能够很容易印刷脱模并且能牢固 地附着在FPC表面,不会出现脱模不良阻塞钢网漏孔或印刷后产生塌陷等不良。
因为载板上装载FPC,FPC上有定位用的耐高温胶带,使其平面不一致,所以FPC的印刷面不可能象PCB那 样平整和厚度硬度一致,所以不宜采用金属刮刀,而应采用硬度在80-90度的聚胺酯型刮刀。 锡膏印刷机最好带有光学定位系统,否则对印刷质量会有较大影响,FPC虽然固定在载板上,但是FPC与载 板之间总会产生一些微小的间隙,这是与PCB硬板最大的区别,因此设备参数的设定对印刷效果也会产生较大 影响。
印刷工位也是防止FPC脏污的重点工位,需要戴手指套作业,同时要保持工位的清洁,勤擦钢网,防止焊 锡膏污染FPC的金手指和镀金按键。
3. FPC的贴片:
根据产品的特性、元件数量和贴片效率,采用中、高速贴片机进行贴装均可。由于每片FPC上都有定位用 的光学MARK标记,所以在FPC上进行SMD贴装与在PCB上进行贴装区别不大。需要注意的是,虽然FPC被固 定在载板上,但是其表面也不可能像PCB硬板一样平整,FPC与载板之间肯定会存在局部空隙,所以,吸嘴下 降高度、吹气压力等需精确设定,吸嘴移动速度需降低。同时,FPC 以联板居多,FPC 的成品率又相对偏低, 所以整PNL中含部分不良PCS是很正常的,这就需要贴片机具备BAD MARK识别功能,否则,在生产这类非整 PNL都是好板的情况下,生产效率就要大打折扣了。
4. FPC的回流焊:
应采用强制性热风对流红外回流焊炉,这样FPC上的温度能较均匀地变化,减少焊接不良的产生。如果是 使用单面胶带的,因为只能固定FPC的四边,中间部分因在热风状态下变形,焊盘容易形成倾斜,熔锡(高温 下的液态锡)会流动而产生空焊、连焊、锡珠,使制程不良率较高。
1)温度曲线测试方法:
由于载板的吸热性不同,FPC上元件种类的不同,它们在回流焊过程中受热后温度上升的速度不同,吸收 的热量也不同,因此仔细地设置回流焊炉的温度曲线,对焊接质量大有影响。比较稳妥的方法是,根据实际生 产时的载板间隔,在测试板前后各放两块装有FPC的载板,同时在测试载板的FPC上贴装有元件,用高温焊锡 丝将测试温探头焊在测试点上,同时用耐高温胶带将探头导线固定在载板上。注意,耐高温胶带不能将测试点 覆盖住。测试点应选在靠近载板各边的焊点和QFP引脚等处,这样的测试结果更能反映真实情况。
2)温度曲线的设置:
在炉温调试中,因为FPC的均温性不好,所以最好采用升温/保温/回流的温度曲线方式,这样各温区的参 数易于控制一些,另外FPC和元件受热冲击的影响都要小一些。根据经验,最好将炉温调到焊锡膏技术要求值 的下限,回焊炉的风速一般都采用炉子所能采用的最低风速,回焊炉链条稳定性要好,不能有抖动。
5. FPC的检验、测试和分板:
由于载板在炉中吸热,特别是铝质载板,出炉时温度较高,所以最好是在出炉口增加强制冷却风扇,帮助 快速降温。同时,作业员需带隔热手套,以免被高温载板烫伤。从载板上拿取完成焊接的FPC时,用力要均匀, 不能使用蛮力,以免FPC被撕裂或产生折痕。
取下的FPC放在5倍以上放大镜下目视检验,重点检查表面残胶、变色、金手指沾锡、锡珠、IC引脚空焊、连焊等问题。由于FPC表面不可能很平整,使AOI的误判率很高,所以FPC一般不适合作AOI检查,但通过借助专用的测试治具,FPC可以完成ICT、FCT的测试。
由于 FPC 以联板居多,可能在作 ICT、FCT 的测试以前,需要先做分板,虽然使用刀片、剪刀等工具也可以完成分板作业,但是作业效率和作业质量低下,报废率高。如果是异形FPC的大批量生产,建议制作专门的FPC冲压分板模,进行冲压分割,可以大幅提高作业效率,同时冲裁出的FPC边缘整齐美观,冲压切板时产生的内应力很低,可以有效避免焊点锡裂。
在PCBA柔性电子的组装焊接过程, FPC的精确定位和固定是重点,固定好坏的关键是制作合适的载板。其次是FPC的预烘烤、印刷、贴片和回流焊。显然FPC的SMT工艺难度要比PCB硬板高很多,所以精确设定工艺参数是必要的,同时,严密的生产制程管理也同样重要,必须保证作业员严格执行SOP上的每一条规定,跟线工程师和IPQC应加强巡检,及时发现产线的异常情况,分析原因并采取必要的措施,才能将FPC SMT产线的不良率控制在几十个PPM之内。
在PCBA生产过程中,需要依靠很多的机器设备才能将一块板子组装完成,往往一个工厂的机器设备的质量水平直接决定着制造的能力。
PCBA生产所需要的基本设备有锡膏印刷机、贴片机、回流焊、AOI检测仪、元器件剪脚机、波峰焊、锡炉、洗板机、ICT测试治具、FCT测试治具、老化测试架等,不同规模的PCBA加工厂,所配备的设备会有所不同。
四.PCBA生产设备
1、锡膏印刷机
现代锡膏印刷机一般由装版、加锡膏、压印、输电路板等机构组成。它的工作原理是:先将要印刷的电路板固定在印刷定位台上,然后由印刷机的左右刮刀把锡膏或红胶通过钢网漏印于对应焊盘,对漏印均匀的PCB,通过传输台输入至贴片机进行自动贴片。
2、贴片机
贴片机:又称“贴装机”、“表面贴装系统”(Surface Mount System),在生产线中,它配置在锡膏印刷机之后,是通过移动贴装头把表面贴装元器件准确地放置PCB焊盘上的一种设备。分为手动和全自动两种。
3、回流焊
回流焊内部有一个加热电路,将空气或氮气加热到足够高的温度后吹向已经贴好元件的线路板,让元件两侧的焊料融化后与主板粘结。这种工艺的优势是温度易于控制,焊接过程中还能避免氧化,制造成本也更容易控制。
4、AOI检测仪
AOI(Automatic Optic Inspection)的全称是自动光学检测,是基于光学原理来对焊接生产中遇到的常见缺陷进行检测的设备。AOI是新兴起的一种新型测试技术,但发展迅速,很多厂家都推出了AOI测试设备。当自动检测时,机器通过摄像头自动扫描PCB,采集图像,测试的焊点与数据库中的合格的参数进行比较,经过图像处理,检查出PCB上缺陷,并通过显示器或自动标志把缺陷显示/标示出来,供维修人员修整。
5、元器件剪脚机
用于对插脚元器件进行剪脚和变形。
6、波峰焊
波峰焊是让插件板的焊接面直接与高温液态锡接触达到焊接目的,其高温液态锡保持一个斜面,并由特殊装置使液态锡形成一道道类似波浪的现象,所以叫"波峰焊",其主要材料是焊锡条。
7、锡炉
一般情况下,锡炉是指电子接焊接中使用的一种焊接工具。对于分立元件线路板焊接一致性好,操作方便、快捷、工作效率高,是您生产加工的好帮手。
8、洗板机
用于对PCBA板进行清洗,可清除焊后板子的残留物。
9、ICT测试治具
ICT Test 主要是*测试探针接触PCB layout出来的测试点来检测PCBA的线路开路、短路、所有零件的焊接情况
10、FCT测试治具
FCT(功能测试)它指的是对测试目标板(UUT:Unit Under Test)提供模拟的运行环境(激励和负载),使其工作于各种设计状态,从而获取到各个状态的参数来验证UUT的功能好坏的测试方法。简单地说,就是对UUT加载合适的激励,测量输出端响应是否合乎要求。
11、老化测试架
老化测试架可批量对PCBA板进行测试,通过长时间等模拟用户使用的操作,测试出有问题的PCBA板。
PCBA外协加工是指PCBA加工厂家将PCBA订单外发给其他有实力的PCBA加工厂家。那么,PCBA外协加工一般有什么要求呢?
一、物料清单
应严格按照物料清单、PCB丝印及外协加工要求进行插装或贴装元件,当发生物料与清单、 PCB丝印不符,或与工艺要求相矛盾,或要求模糊不清而不能作业时,应及时与我公司联系,确认物料及工艺要求的正确性。
二、防静电要求
1、所有元器件均作为静电敏感器件对待。
2、凡与元器件及产品接触人员均穿防静电衣、佩戴防静电手环、穿防静电鞋。
3、原料进厂与仓存阶段,静电敏感器件均采用防静电包装。
4、作业过程中,使用防静电工作台面,元器件及半成品使用防静电容器盛放。
5、焊接设备可靠接地,电烙铁采用防静电型。使用前均需经过检测。
6、PCB板半成品存放及运输,均采用防静电箱,隔离材料使用防静电珍珠棉。
7、无外壳整机使用防静电包装袋。
三、元器件外观标识插装方向的规定
1、极性元器件按极性插装。
2、丝印在侧面的元器件(如高压陶瓷电容)竖向插装时,丝印朝右;横向插装时,丝印朝下。丝印在顶部的元器件(不包括贴片电阻)横向插装时,字体方向同PCB板丝印方向;竖向插装时,字体上方朝右。
3、电阻卧式横向插装时,误差色环朝右;卧式竖向插装时,误差色环朝下;电阻立式插装时,误差色环朝向板面。
四、焊接要求
1、插装元件在焊接面引脚高度1.5~2.0mm。贴片元件应平贴板面,焊点光滑无毛刺、略呈弧状,焊锡应超过焊端高度的2/3,但不应超过焊端高度。少锡、焊点呈球状或焊锡覆盖贴片均为不良;
2、焊点高度:焊锡爬附引脚高度单面板不小于1mm,双面板不小于0.5mm且需透锡。
3、焊点形状:呈圆锥状且布满整个焊盘。
4、焊点表面:光滑、明亮,无黑斑、助焊剂等杂物,无尖刺、凹坑、气孔、露铜等缺陷。
5、焊点强度:与焊盘及引脚充分润湿,无虚焊、假焊。
6、焊点截面:元件剪脚尽可能不剪到焊锡部分,在引脚与焊锡的接触面上无裂锡现象。在截面处无尖刺、倒钩。
7、针座焊接:针座要求底部贴板插装,且位置端正,方向正确,针座焊接后,底部浮高不超过0.5mm,座体歪斜不超出丝印框。成排的针座还应保持整齐,不允许前后错位或高低不平
五、运输
为防止PCBA损坏,在运输时应使用如下包装:
1、盛放容器:防静电周转箱。
2、隔离材料:防静电珍珠棉。
3、放置间距:PCB板与板之间、PCB板与箱体之间有大于10mm的距离。
4、放置高度:距周转箱顶面有大于50mm的空间,保证周转箱叠放时不要压到电源,特别是有线材的电源。
六、洗板要求
板面应洁净,无锡珠、元件引脚、污渍。特别是插件面的焊点处,应看不到任何焊接留下的污物。洗板时应对以下器件加以防护:线材、连接端子、继电器、开关、聚脂电容等易腐蚀器件,且继电器严禁用超声波清洗。
七、所有元器件安装完成后不允超出PCB板边缘。
八、PCBA过炉时,由于插件元件的引脚受到锡流的冲刷,部分插件元件过炉焊接后会存在倾斜,导致元件本体超出丝印框,因此要求锡炉后的补焊人员对其进行适当修正。
评论